Advantages of Rolled Ring Forging
Forging, a centuries-old technique, has been an integral part of metalworking history. Over the years, the forging process has evolved, offering various methods suitable for different applications. Among all these, rolled ring forging stands out due to its distinct benefits and versatility. This process involves piercing a hole in a billet and subsequently rolling it into a thin ring. The advantages of this technique are manifold, from its cost-effectiveness to the quality of products it yields.
What is Rolled Ring Forging?
Rolled ring forging is a specialized metalworking process used to produce seamless, circular rings of various sizes and cross-sectional profiles. It starts with a circular form of metal, a hole punched in its center, creating a donut-like shape component. This is then heated until malleable and rolled under pressure between two concentric rings until the desired ring diameter and thickness are achieved. Rolled ring forging is widely utilized in industries like aerospace, automotive, and energy due to its efficiency and the high-quality rings it produces.
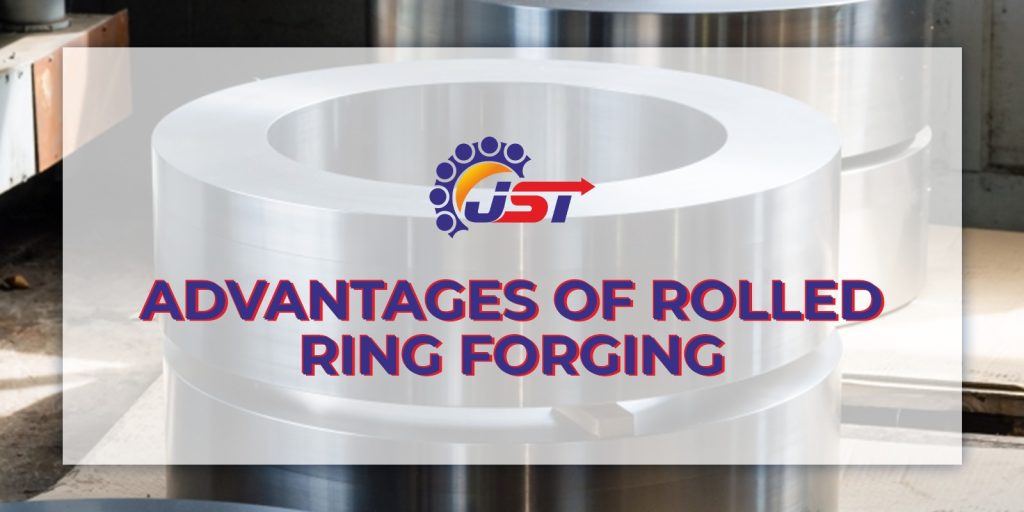
Benefits of Rolled Ring Forging:
Broad Range of Shapes and Sizes –
The rolled ring forging process offers a substantial degree of flexibility in terms of shapes and sizes. Be it a small washer-like part or a large diameter bearing ring, this process can craft it. It can produce parts with diameters of a few inches to over 300 inches and weigh from a single pound up to over 25 tons.
Cost-effective Production –
Compared to other forging or casting methods, rolled ring forging often proves to be more cost-effective. The process uses starting shapes that are close to the shape of the final ring, reducing waste and the need for extensive machining. As the raw material input is more accurately used, producers often save costs, which can be passed on to consumers.
Enhance Strength and Durability –
One of the greatest benefits of the rolled ring forging process is the enhanced strength and durability of the products. The process modifies the grain structure of the metal, often making it more compact and aligned, enhancing its resistance against fatigue and impact. The grain refinement ensures that the final product has a longer service life and can withstand challenging conditions.
Uniformity of Composition –
Ring Rolling produces rings that have a uniform and smooth surface, devoid of the defect one might find in castings, like porosity or shrinkage cavities. The uniformity ensures better performance and reduces the risk of unforeseen equipment failures in critical applications.
Versatility in Material Use –
Another advantage of this process is its ability to handle a vast range of materials. From alloy steels, carbon, and stainless steel to aerospace metals like Inconel, the process can manage various metals, each offering unique properties to the finished products.
Improved Heat Tolerance and Resistance –
Products manufactured using ring-rolled forging demonstrate improved heat tolerance. This makes them ideal for applications that demand materials to withstand extreme temperatures, like jet engines, turbine engines, and other high-temperature applications.
Economical Mass Production –
While forging a ring is a skill-intensive task, once properly set up, the forging process can be replicated for mass production swiftly. The economies of scale can be achieved, making it beneficial for large projects or industries that require standardized parts in bulk.
Reduced Machining Requirements –
Due to the precision and accuracy of the heat treatment, the resultant product often requires less machining compared to those produced by other methods. This not only reduces production time but also minimizes the waste produced.
Enhanced Metallurgical Properties –
The forging process inherently refines the metallurgical microstructure of the material. As a result, forging components often exhibit enhanced metallurgical properties, including better flexibility and an increased capacity to withstand wear and tear.
Sustainability –
Given that rolled ring forging utilizes materials efficiently and minimizes waste, it can be seen as a more sustainable manufacturing method. In an age where industries are increasingly conscious of their environmental footprints, this factor can be of high importance.
Also Read – Growing Needs of the Automotive Industry
Wrapping up
The rolled ring forging, with its myriad of advantages, is a testament to how innovation and technology can refine age-old techniques. Industries ranging from aerospace and automotive to manufacturing and energy can harness the benefit of this method to produce high-quality, durable, and efficient components.
The strategic amalgamation of cost-effectiveness, strength, and flexibility makes forging a go-to choice for many applications. As industries evolve, the reliance on processes that assure quality and durability, like rolled ring forging, will only continue to grow.
Recent comments