Ring forging process is a way to make rings from metal by heating it until it’s soft and then pressing it into shape. This method creates very strong rings without any gaps or joins. Different metals, like carbon steel, stainless steel, and aluminium, are used for making specific kinds of items. Milling is another method where a machine with spinning blades shapes materials into detailed designs. As technology improves, both these methods are getting better, producing more accurate results, using resources wisely, and being more environmentally friendly. The type of material chosen for these methods is super important because it affects the quality of the end product.
This article aims to explore deeper into how ring forging and milling work and why the choice of material is crucial in today’s manufacturing world.
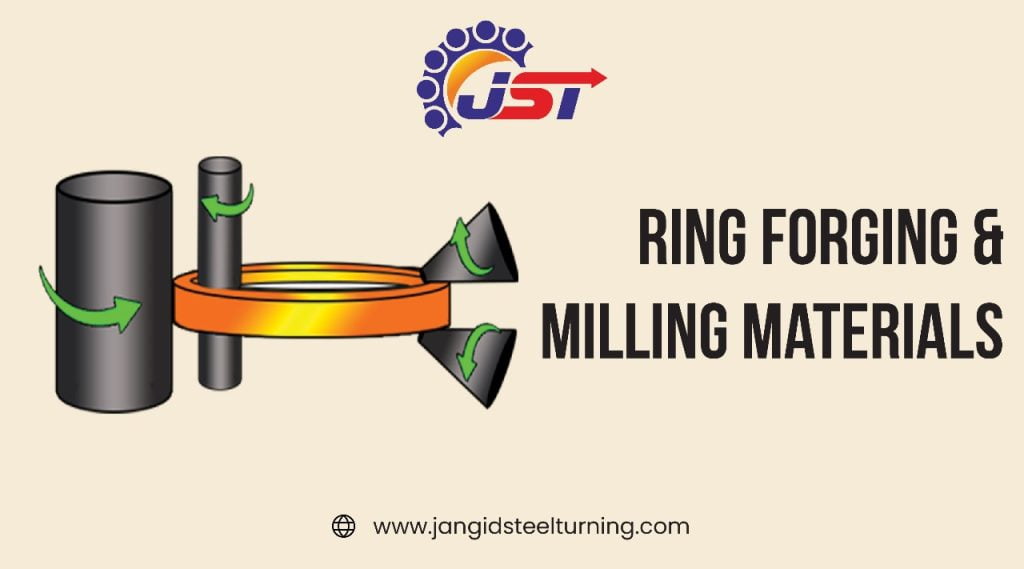
Introduction to Ring Forging –
Ring Forging is a specialized process followed by the forging industry, aiming at the creation of rings of different sizes. It may range from a few inches in diameter to over 30 feet. These rings are integral components in various industries like aerospace, power generation, and machinery, to name a few.
Introduction to Milling –
Milling is like carving. It uses spinning blades to cut and shape materials into specific designs. It’s a way to accurately make complicated shapes that would otherwise take a long time to create.
Process of Ring Forging –
The process starts by making a hole in a metal circle. This metal circle is then shaped into a ring. To make the metal soft and easy to shape, it’s heated. Once soft, it’s pressed and shaped into a solid ring without any joints. This whole method uses a lot of heat and pressure to turn a metal circle into a strong ring.
Advantages of Ring Forging –
The benefits of ring forging extend beyond ring forming. The process provides exceptional grain flow, making the rings highly durable. It also ensures a high strength-to-weight ratio, making forged rings preferable in industries demanding robust components.
Integrity – Forged rings possess high directional strength, ensuring durability.
Versatility – Can be tailored to fit a variety of geometric configurations.
Cost-effective – Reduces the need for welding multiple small components.
Materials used in Ring Forging and Milling –
Choosing the right material is highly important in forging processes, as it determines the ring’s quality, durability, and application viability. Some prominent materials are:
Carbon steel is known for its strength and versatility and is often used in forging rings. An alloy of iron and carbon steel is hailed for its strength. Its mechanical properties can be enhanced further through heat treatments, making it adaptable to various needs.
Stainless steel comes with superior resistance to corrosion and high-temperature endurance. Renowned for its resistance to rust and tarnishing, stainless steel’s unique properties stem from the addition of chromium. This metal’s adaptability makes it suitable for applications demanding longevity and hygiene.
Alloy steel is used when additional attributes like improved hardness or corrosion resistance are required. By adding elements like nickel, manganese and chromium, alloy steel offers a tailored set of properties. Depending on the combination, alloy steel can possess increased hardness, toughness, etc.
Aluminium, being lightweight yet strong, is crucial for the aerospace and automobile sectors. Esteemed for its lightweight nature, aluminium offers commendable strength, making it a staple in the aerospace and automotive sectors. It’s also celebrated for its non-toxic nature, thermal conductivity, and resistance to corrosion.
Titanium is vital for aerospace applications, is resistant to corrosion, and can withstand high temperatures. Renowned for its excellent strength-to-weight ratio, titanium offers twice the strength of aluminium and rivals many forms of steel. Its biocompatibility makes it a favoured choice in the medical realm.
The Future of Milling and Ring Forging –
New tech tools, like smart milling machines and computer predictions, are making big changes in how forging works. Also, as companies try to be kinder to the environment, they’re looking at creating new mixed metals and materials. These new materials are not just better for nature but also help improve the final product. Everyone is working to find ways that are better for our planet while still making great products. So, as technology keeps improving, we’ll see even more changes and advances in this field, which is exciting for the future.
Also Read – Growing Needs of the Automotive Industry
Wrapping up –Ring forging and milling form the core of many different industries, driving economies and technological advancements. The meticulous selection of materials, understanding their properties, and leveraging them aptly underpins the success of these processes. As the world depends more towards sustainability and precision, the realms of ring forging and milling are poised for further innovations, ensuring they remain pillars of modern manufacturing.