Different Types of Forging Processes
What are the Different Types of Forging Processes?
Forging is a manufacturing process where metal is pressed, pounded, or squeezed under great pressure into high-strength parts. The process has been practised for centuries and has been practised for centuries and has been instrumental in shaping the history of human civilization, from the crafting of rudimentary weapons to the creation of intricate components of modern industries. As industries and technologies have advanced, so have the methods and processes of forging. Let’s dive into understanding the different types of forging processes prevalent today.
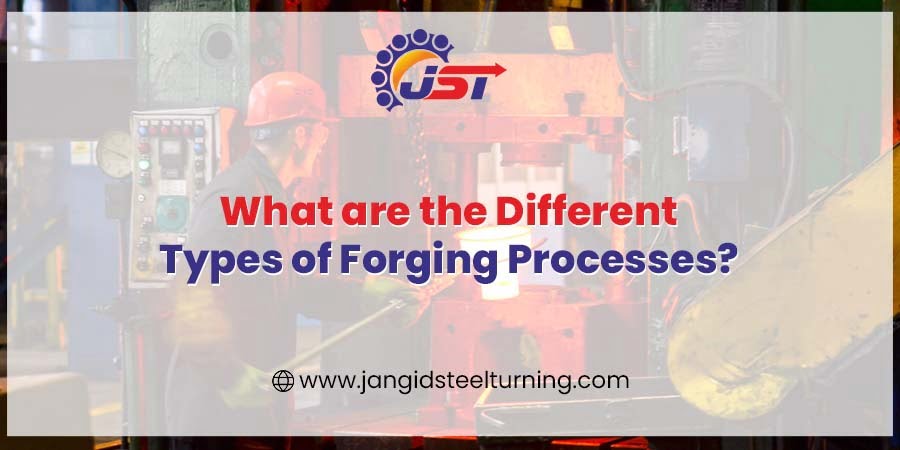
Open Die Forging –
Also known as free forging, open die forging involves the placing of a metal piece between multiple dies that don’t enclose the metal entirely. The dies hammer and stamp the material to achieve the desired shape. The method offers flexibility in forging large and complex shapes, often used for shafts, discs, and customized parts.
Application – Large yet simple components like cylinders, discs, hubs, and shafts.
Advantages –
- Superior strength due to reduced chances of voids.
- Improved microstructure.
- Greater flexibility in shaping.
Closed Die Forging –
Contrary to open-die forging, closed-die forging, also known as impression die forging, involves two or more dies that contain a precut profile of the desired components. The metal undergoes plastic deformation, filling the die cavities to achieve the shape. The die contains a precut profile of the desired component, ensuring the metal fills these cavities perfectly.
Application – Complex shapes in sectors like automotive, aerospace, and agriculture.
Advantages:
- High accuracy.
- Excellent surface finish.
- Economical for large production runs.
Roll Forging –
The process involves compressing a heated metal piece between two counter-rotating rolls. It has one or more grooves that help shape the metal. As the metal passes through, it takes the form of the roll’s impressions. Roll forging is highly efficient, reduces wastage, and is pivotal in producing axles, leaf springs, and tapered rods.
Application – Axles, tapered rods, and leaf springs.
Advantages –
- Efficient material usage.
- Reduction in the need for machining.
- Suitable for mass production.
Swaging –
Swaging uses a machine to reduce the diameter of a rod or tube by forging the piece into a confining die or die’s. The process can be done cold or hot, depending on the material and end product’s requirements. Employed for both solid and tubular materials, swaging refines, and contour sections for precise fitments.
Application – Pointed rod tips, weapon barrels and cable fittings.
Advantages –
- Precise diameter control.
- Increased strength of the worked section.
- Improved grain structure.
Upset Forging –
The process increases the diameter of a particular section of a rod or wire by compressing its length. The machines used for this process are called upsetters. Predominantly used for creating heads on components like bolts or nails, upset forging optimizes material utilization and assure uniformity and strength in forged part.
Application – Bolt heads, screws, and other fasteners.
Advantages –
- Enhanced localized diameter
- Improved material properties
- Effective for creating heads on nails and bolts
Seamless Rolled Ring Forging –
The process involves the production of seamless rings. The Ring Forging Process begins with the rounding of a billet that is pierced to form a hollow ring. It’s then heated and rotated to reduce its wall thickness and increase the ring’s diameter. The process ensures a seamless, strong ring, widely used in aerospace, engineering, and bearing applications for its structural integrity.
Applications – Large Bearings, high-pressure flanges, and tall gears.
Advantages –
- Greater strength and resistance.
- Cost-effective for large-scale production
- Versatility in ring size and material.
Press Forging –
Besides using impact blows, press forging uses a slow, continuous pressure to shape metal. The compressive force applied by the press can be vertical or horizontal. Employing hydraulic or mechanical presses, press forging ensures precise shapes, consistent material distribution, and improved structural integrity. It is ideal for producing intricate components in industries like automotive and machinery.
Application – Airplane parts, hand tools, and hardware.
Advantages –
- High precision and accuracy
- Improved structural integrity
- Greater material distribution
Also Read – What is the Heat Treatment Process?
Wrapping up –With time, the forging business has changed, honing its techniques to satisfy the needs of the contemporary engineering and manufacturing industries. Every kind of forging technique has special benefits that make it appropriate for use. Industries can maximize the functionality, robustness, and affordability of their metal components by making educated judgements based on their understanding of the various forging methods.
Recent comments