We understand the importance of innovation and professionalism
Started in 1987, the Jangid Steel Turning company is still a full-service structural engineering firm. In addition to constructing Forged, Machined and Heat-Treated Bearing Races, we also produce bespoke quality auto components. A privately-owned firm was founded with the goal of manufacturing bearing races using tubes and rods conforming to top quality requirements financially efficiently. Being a prominent automotive parts maker in India seems to be a result of our commitment to quality and development. Our manufacturing companies, which have a generating capacity of 7.2 million rings and automobile parts per year, are some of the best in the market. Our goal is to achieve excellence by maintaining a strong and positive correlation.
Every growing moment, motion technology is driven toward superiority by invention, accuracy, and transformation. And this is how JST are viewed in the motor industry. The company seems to be a significant maker of forging and machining elements in India, with its headquarters in JAIPUR. That’s a top strategic partner, producing high-quality, world-class, customized automotive parts and bearing races for such a global customer base. Over such a four-decade period, we’ve accumulated knowledge of manufacturing techniques for different forgings and machines. We’ve developed extensive competence in the production of transmitting components, electronic components, chassis parts and bearing races at JST.
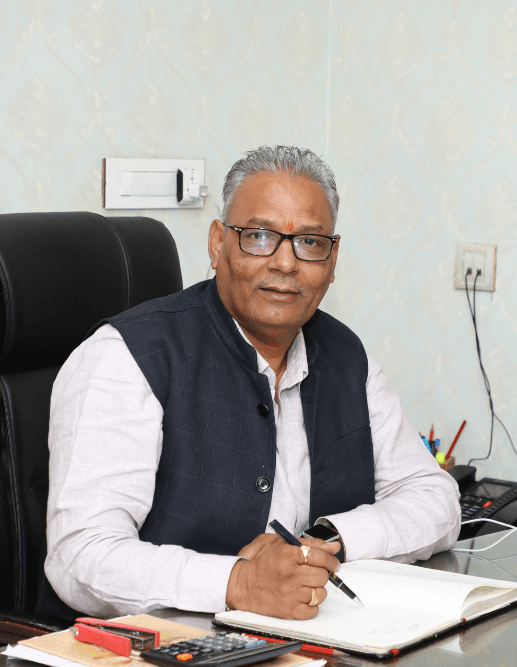
Constantly focusing on technological innovations, customized approaches, and harnessing the power of diverse technical abilities, we have never wavered in our commitment to excellence. It has been a long and successful run for Machinery as a nationally recognized participant. Throughout the coming years, it aspires to become a leading company.
It is capable of producing procedures and technologies that are precise, consistent, and cost-effective because of its in-house seasoned group of skilled and technologically advanced people, including an automated lab and machine construction shop. Our talent management center contains a range of materials that ensure that our employees develop consistently.
JST manufactures components in all imaginable forms, be it bars, or forging, giving consumers the choice to select products that satisfy. Product development modifications can be accommodated in a timely manner thanks to flexible methods. Our in-house innovation center significantly reduces development delay periods.
The JST does have the capacity to forge pieces in a near-net shape, resulting in a greater potential yield for products and substantial material reductions. Components with lower production usage and optimal grain motion can be produced using a method that includes forging on even a Hatebur and cold forming choices.
Over the last several decades, the major automobile sector has grown steadily. As shown in a recent projection, the business would be worth the US $2 million by FY26. India’s automotive parts sector contributes 2.3 percent to the country’s GDP.
JANGID STEEL TURNING in India is the top organization supporting Indian automotive component companies’ interests. Its nearly 850 affiliates account for more than 85% of the structured automotive parts industry’s revenue.
JST is such a well-known and respected worldwide company, producing precision machining process components and systems. It is used in a variety of industries, including automobiles, earthmoving, hydraulic systems, railroads, defense, and advanced manufacturing, to meet international and domestic demands.
JST is in direct engagement in international trade, technical advancement, quality improvement, and data collection and communication has made it a critical accelerator for component companies’ growth in India. Other operations involve attending global trade shows, sending commercial delegations abroad, and publishing.
Today, the company is regarded as being one of the most trusted and dependable suppliers in the market. In respect of monetary throughput, the company has achieved unrivaled achievement.
We stay current with the latest applications and building technologies
To nurture quality at each and every stage of the manufacturing process, We follow stringent Q.C. Policy which adheres to international quality standards. We are IATF16949:2016 Certified, TUV. Attention to proper fit and functional Engineering, produces consistent results, batch after batch winning TRUST & CONFIDENCE of our valued customers.